900 packages a day
Kaj’s little workshop at home on his farm near Ellös has grown. By 1981, it had grown so much that the entire operation had to move to new premises in the nearby industrial area.
However, the number of parts held in stock increased in line with the recruitment of new members of staff, and after just a couple of years Kaj had outgrown his new building – it was time for the first of several extensions. Today, Olsson Parts has many thousand square metres at its disposal. The storage space and the capacity are constantly being expanded, nowadays mainly upwards, with the aid of modern, ergonomic product hoists.
– We now stock more than 30,000 different parts, which is many thousands more than we did three decades ago. At that time, we had one freight provider on one market, whereas now we have seven world-leading freight providers on five markets, states Patrick Winter, Warehouse and Logistics Manager.
A large warehouse places considerable demands as regards good warehouse logistics, and optimisation and stock management are constantly being tightened up, both physically and administratively. Patrick believes that this is a major part of the recipe for success:
– Committed and knowledgeable employees, along with modern warehouse logistics where we prioritise the processing of orders on the same day, are crucial for our success. We have introduced two shifts in order to handle more orders per day. As a result, we are able to pack and dispatch an average of 900 packages every day.
High ceilings in the warehouse
The B-hall at the warehouse is a hive of activity. Cornelia and Christian are unpacking air filters, while Lotta is repacking clamps and O-rings. Karin starts up the forklifts and gets ready to receive the first delivery of the week. Today, around ten pallets will have to be brought in and lifted up onto the shelves, pending unpacking and registration in the system.
The atmosphere in the team is great and there is a lot of laughter.
– This is genuine teamwork. If I don’t do my job, the others can’t do theirs. We have to back each other up and follow the procedures that have been established. If something isn’t working properly, we adjust the flow a little and identify new, improved solutions, says Karin.
Even the smallest nut has to be processed and be entered in the system and – not least – be placed on shelves and in hoists so that the team’s colleagues in dispatch can do their job. In the hall next door, work is also proceeding at full tilt. All the customer orders are handled here, everything from small deliveries by post to large deliveries on pallets for collection by companies such as PostNord, Schenker and DHL.
– It is our responsibility to ensure that our customers receive their orders quickly and smoothly, says Julia, who has just dealt with a batch of orders for onward delivery to a customer. Julia, Cornelia, Lotta, Christian and their colleagues handle up to 1,000 orders a day. Mondays are usually the busiest day of the week.
There is a humming noise in one of the warehouse aisles as a forklift approaches. It’s Gabriel, who is about to lift down a pallet of engine overhaul kits.
– Everyone who works in the warehouse is offered the chance to receive forklift training. The highest shelves are many metres tall, and so things run more smoothly if you can resolve situations yourself without having to ask someone else for help, say Gabriel. He is actually supposed to be working the evening shift today, but has come in a little earlier to help with a large incoming delivery.
– There’s nothing unusual about that – we help each other out here.
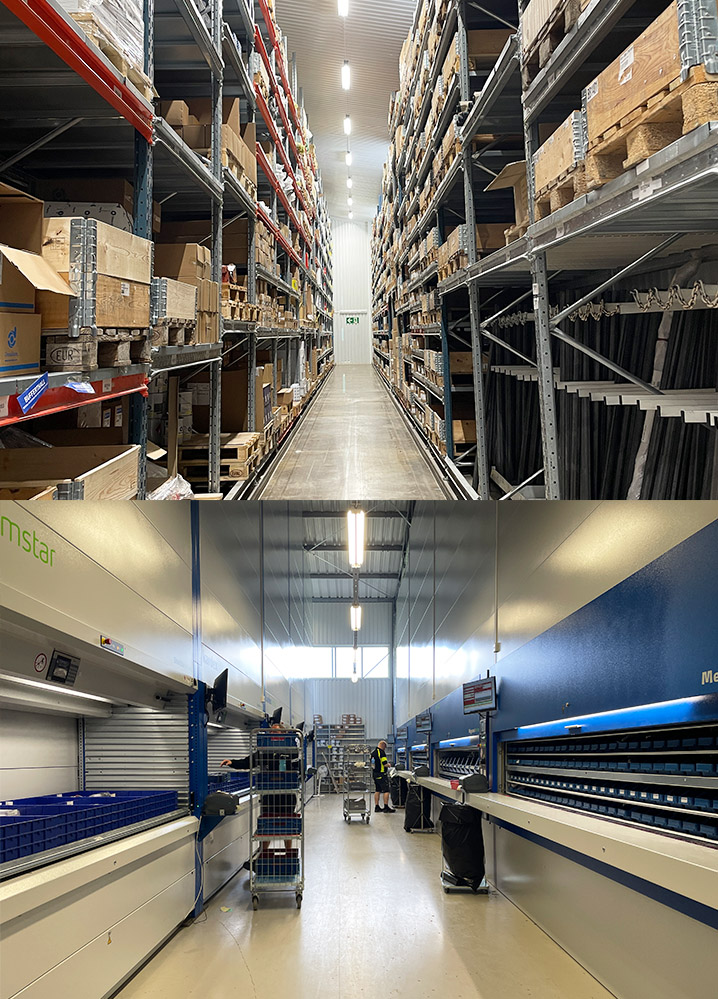